ElectroFin ROI
Cost Savings & Specifying ElectroFin® E-Coat
In mild, non-coastal environments, aluminum-fin coils pre-coated with an epoxy offer a bit more protection than an uncoated coil and can be more economical than copper or e-coated coils. Coatings suppliers sometimes hedge on how much their product adds to the service life of equipment, saying their coating extends the life of a coil “several times compared to an uncoated coil.” ElectroFin® E-Coat is specifically formulated and optimized to lengthen equipment service life by four to five times and have less than 1% impact on the thermal efficiency of the coils it protects.
Major HVAC/R OEMs approve the use of ElectroFin® E-Coat and many OEMs approve of Insitu® Spray Applied Coating for their systems. ElectroFin® E-Coat and Insitu® Spray Applied Coating deliver other benefits as well:
- It can help to reduce energy consumption and can help new construction projects attain LEED certification by the U.S. Green Building Council.
- In densely populated urban areas, vehicle exhaust trapped by high-rise buildings can create a corrosive micro-environment.
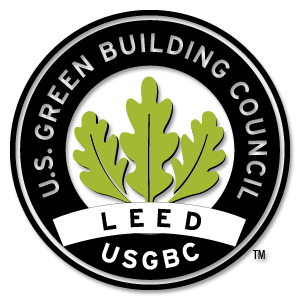
EFinSM Pro Shield™ Program- the Ultimate Coating Protection
EFINSM Pro Shield™ Program – Ultimate Coating Protection with the Required Warranty The EFINSM Pro Shield™ Program is a multi- layer coating protection program for Round Tube Plate Fin (RTPF) and Microchannel Heat Exchangers, where the customer chooses the level of warranty protection desired.
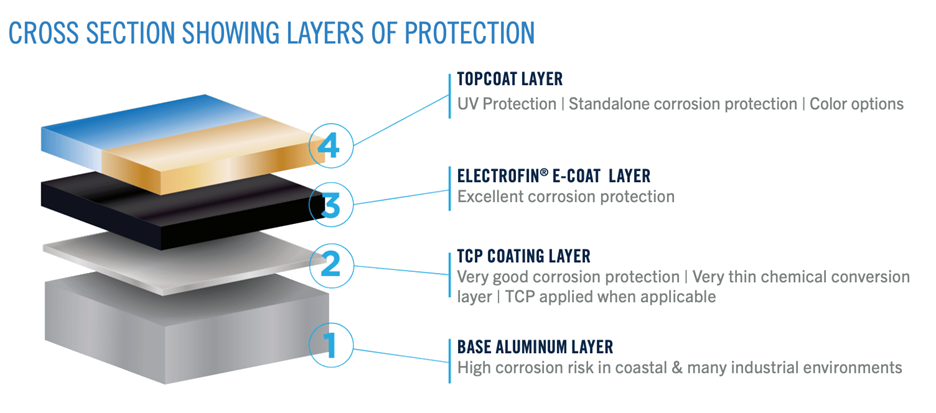
ELECTROFIN® E-COAT TECHNOLOGY Our unique process provides an electro-deposition coating that involves epoxy paint particles evenly suspended in deionized water. When electrically charged, the paint particles migrate to and bond with aluminum, copper, and other conductive metal surfaces that form the heat exchanger coils. Resin and pigment migrate to the part, and an organic uniform film is irreversibly deposited. This unique phenomenon is particularly important for tiny cavities where fin and tube joints, high fin densities, and enhanced fins are present. The charged molecules are drawn to the metal and form an even, continuous film over the entire surface. This coating process creates a smooth, consistent, and flexible coating that penetrates deep into all coil cavities and covers the entire coil assembly, including the fin edges.
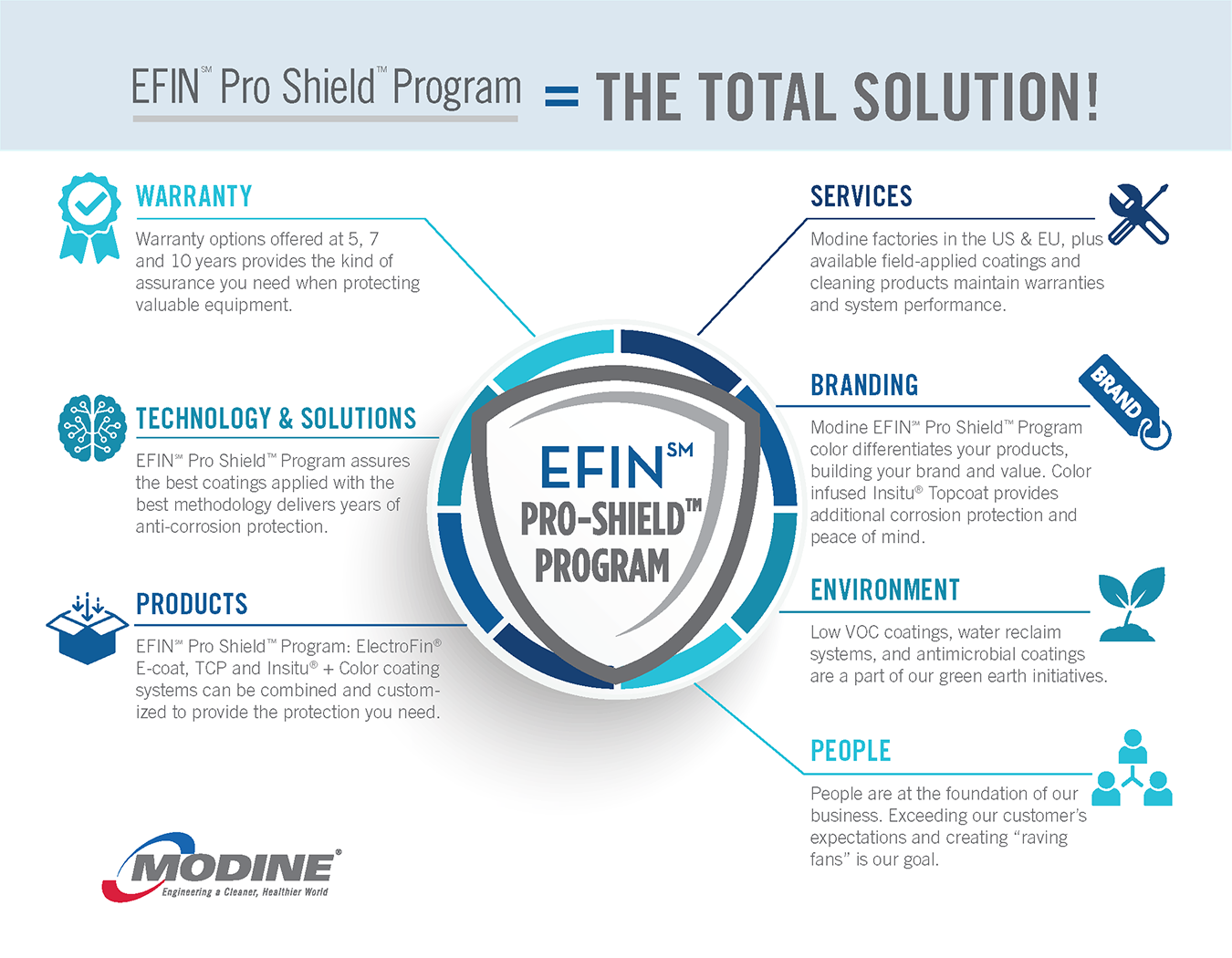
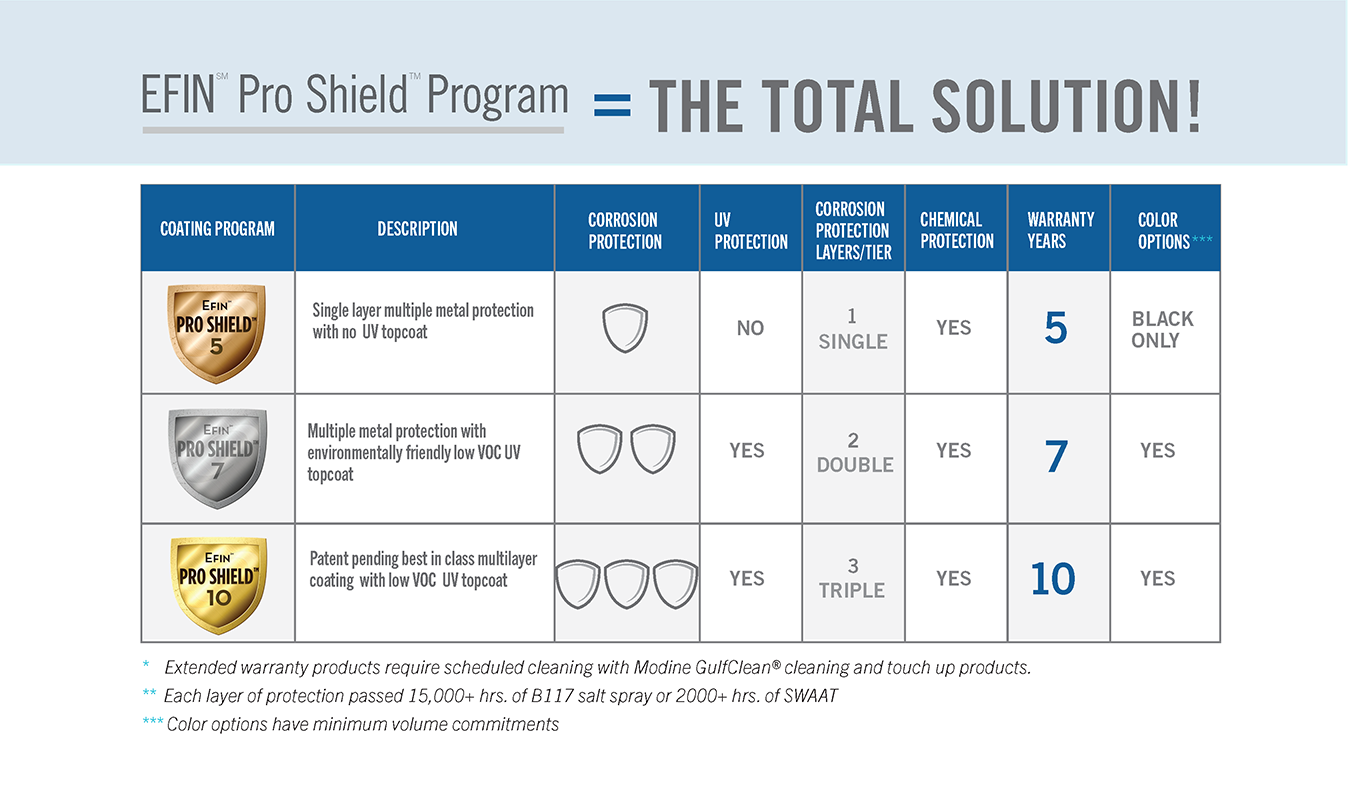
***TCP applied when applicable
Specifying ElectroFin® E-Coat
ElectroFin® E-Coat is the number-one choice of OEMs for heat transfer coil corrosion protection. All major OEM brands offer it for their customers, who value its extra protection and cooling efficiency. Typically, the inclusion of ElectroFin® E-Coat in the manufacturing stage adds about two weeks to the order/delivery cycle.
Key to keeping your company’s construction or renovation timetables on schedule is reaching out to your general contractor early on. Have your contractor break out the cost of adding ElectroFin® E-Coat to its overall bid. Some contractors may be reluctant to do so because they believe that including the cost of any factory-applied coating (even separately) will make their bid less competitive.
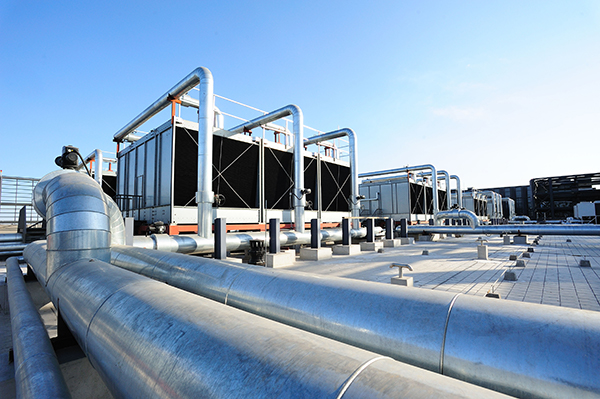
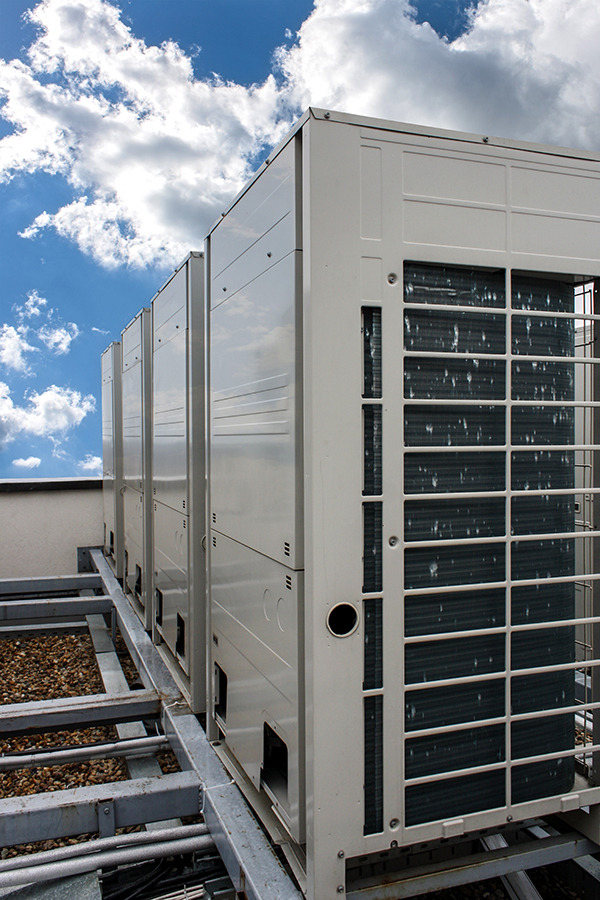
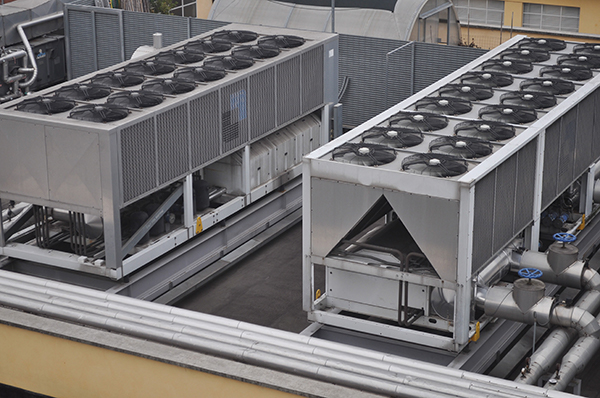