GulfCoat® Corrosion Coatings
Protect Expensive HVAC/R Equipment from Corrosion!
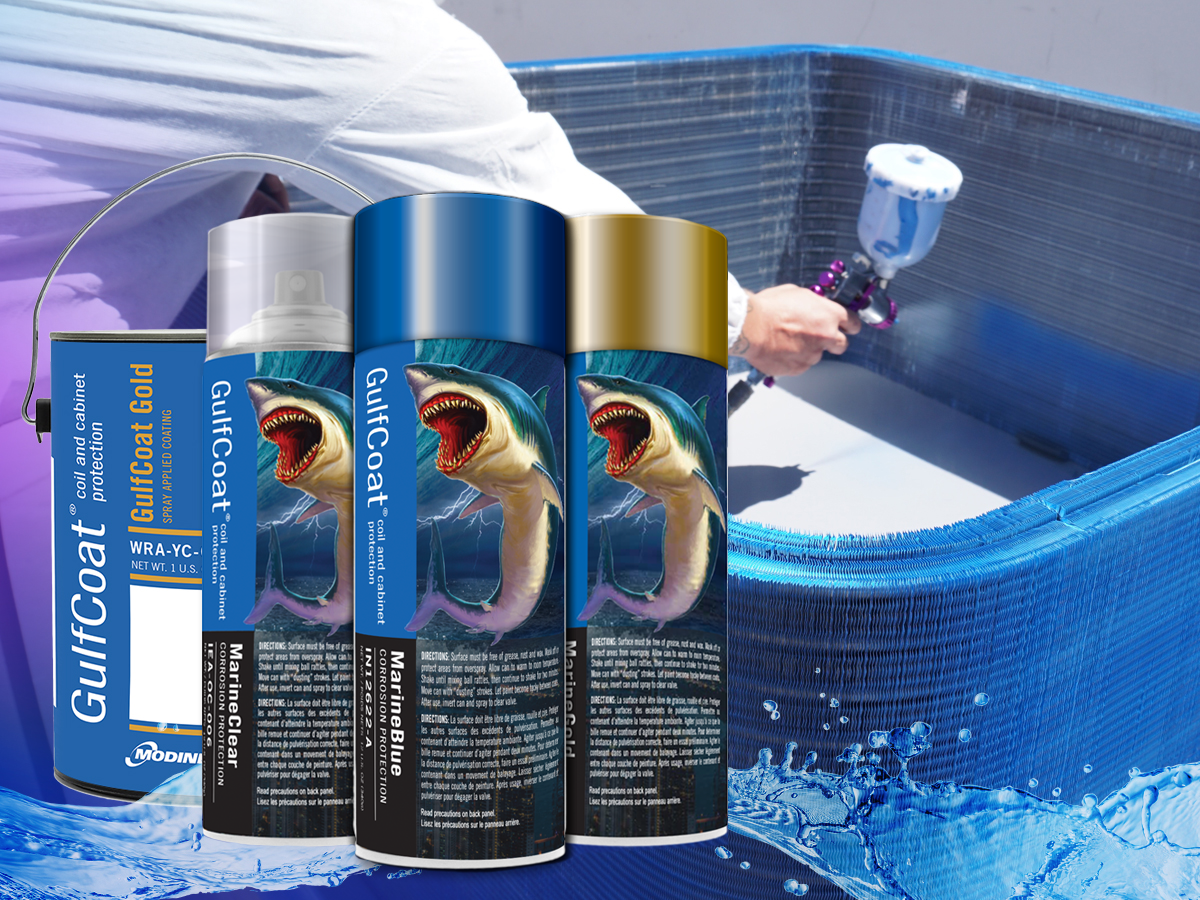
GulfCoat® Corrosion Coatings were developed in response to a demand for a protective, anticorrosion coating that could be applied to small units at installation time or later. GulfCoat® Corrosion Coatings are formulated to resist corrosion with improved adhesion, plus moisture and UV resistance. Applying a GulfCoat® Corrosion Coating protects HVAC/R systems and equipment so they will enjoy a longer service life and lower the total cost of ownership, while maintaining a higher level of efficiently throughout its life cycle.
Specially formulated to reach deep into the evaporator and condenser heat transfer coil fins, GulfCoat® Corrosion Coating penetrates deeply to ensure complete coverage when properly applied. It sprays on evenly without excessive buildup or oversaturation that can clog vital portals and air passages and reduce system efficiency. GulfCoat® decelerates corrosion on the non-ferrous metal fins and tubes, extending the HVAC/R equipment life while helping to maintain good air flow efficiencies along with easier coil cleaning and maintenance.
Benefits
- Easy to apply on-site or at your premises
- Coating Flexibility for improved air flow
- Provides effective moisture barrier
- Provides for easy maintenance
- Reduces major maintenance and replacement costs – especially in corrosive environments
Corrosion Resistance
GulfCoat® Corrosion Coatings have a robust synthetic multi-polymer resin backbone that’s suitable for most environmental conditions and will maintain its appearance after many years of exposure to the elements.
UV Resistance
Enhanced built-in UV inhibitors form a protective barrier throughout the coating film. As a result, UV degradation of individual polymer molecules are reduced, and the film integrity maintained.
Gloss Retention
GulfCoat® Corrosion Coatings provide a high gloss finish that is smooth, limits dirt and debris buildup and allows for easy equipment cleaning.
Two Formulations to Get The Job Done!
Spray Applied OR Aerosol Spray
Whether using aerosol can or spray equipment application, both versions are available in three colors – Blue, Clear, and Gold. These anti-corrosion coatings are specifically designed for protecting HVAC/R coils, components, and cabinets.
Spray Applied
For larger HVAC/R equipment installations. Should be applied with a recommended spray gun/spray equipment.
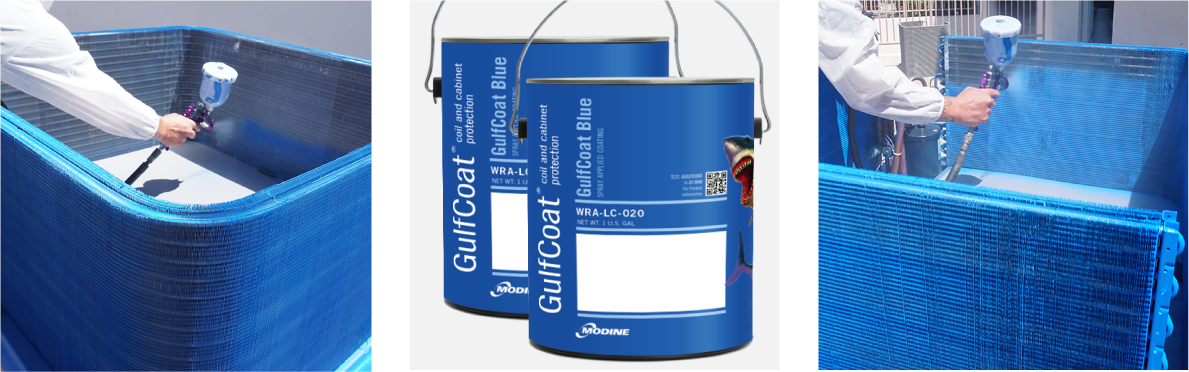
Equipment Applications
- Heat Exchanger Coils (water, condenser, evaporator, DX)
- Mini-Splits
- Packaged Rooftops
- Condensing Units
- Modular Air-handlers
- Air-Cooled Chillers
- HVAC/R cabinet interiors and exteriors
Environmentally Friendly
- Compliant for use in all states
- Contain low Volatile Organic Compounds (VOCs)
- Non-ozone depleting chemicals
- Non-flammable (flashpoint >201°F/94°C)
- Free from Hazardous Air Pollutants (HAPs)
- Free from SARA Section 313 listed chemicals
- No Perfluroalkoxy Alkanes (PFAS)
- EU and REACH compliant
Application and Performance Characteristics
GulfCoat® Corrosion Coatings applied to HVAC/R coil and components shall have a water-based synthetic polymer coating spray-applied with no material bridging between fins. The spray coating process should ensure a uniform dry film thickness of 10-36 μm (0.4 -1.4 mils) and meet 5B rating for crosshatch adhesion per ASTM D3359. Corrosion durability shall be confirmed through testing to no less than 5000 hours salt spray resistance per ASTM B117 using aluminum test coupons.
Performance Properties
Test | ASTM Method | Results |
---|---|---|
Salt Spray | B117 | Exceeds 5000 Hours |
UV Resistance | D4587 | 1000 Hours |
Direct Impact | D2794 | Passed #160 |
Pencil Hardness | D3363 | HB-F |
Cross Hatch Adhesion | D3359 | 5B |
Humidity | D2247 | 1000 Hours |
Mandrel Bend | D522M | Pass 1/4” (6.35mm) |
Aerosol Spray
Handy aerosol cans eliminate the need for spray equipment and make application at installation time or later easy.
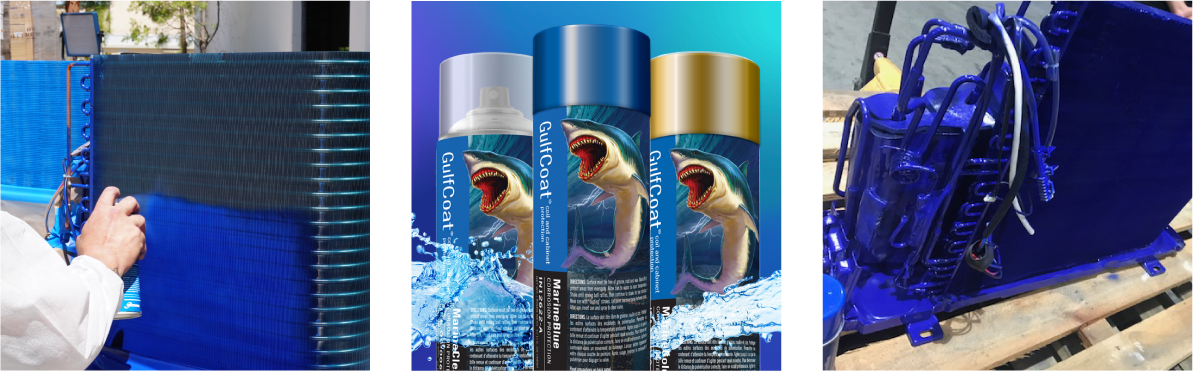
Equipment Applications
- Heat Exchanger Coils (water, condenser, evaporator, DX)
- Mini-Splits
- Packaged Rooftops
- Condensing Units
- Modular Air-handlers
- Air-Cooled Chillers
- HVAC/R cabinet interiors and exteriors
Environmentally Friendly
- Compliant for use in all states
- Contain low Volatile Organic Compounds (VOCs)
- Non-ozone depleting chemicals
- Non-flammable (flashpoint >201°F/94°C)
- Free from Hazardous Air Pollutants (HAPs)
- Free from SARA Section 313 listed chemicals
- No Perfluroalkoxy Alkanes (PFAS)
- EU and REACH compliant
Application and Performance Characteristics
GulfCoat® Corrosion Coatings applied to HVAC/R coil and components shall have a water-based synthetic polymer coating spray-applied with no material bridging between fins. The spray coating process should ensure a uniform dry film thickness of 10-36 μm (0.4 -1.4 mils) and meet 5B rating for crosshatch adhesion per ASTM D3359. Corrosion durability shall be confirmed through testing to no less than 5000 hours salt spray resistance per ASTM B117 using aluminum test coupons.
Performance Properties
Test | ASTM Method | Results |
---|---|---|
Salt Spray | B117 | Exceeds 5000 Hours |
UV Resistance | D4587 | 1000 Hours |
Direct Impact | D2794 | Passed #160 |
Pencil Hardness | D3363 | HB-F |
Cross Hatch Adhesion | D3359 | 5B |
Humidity | D2247 | 1000 Hours |
Mandrel Bend | D522M | Pass 1/4” (6.35mm) |